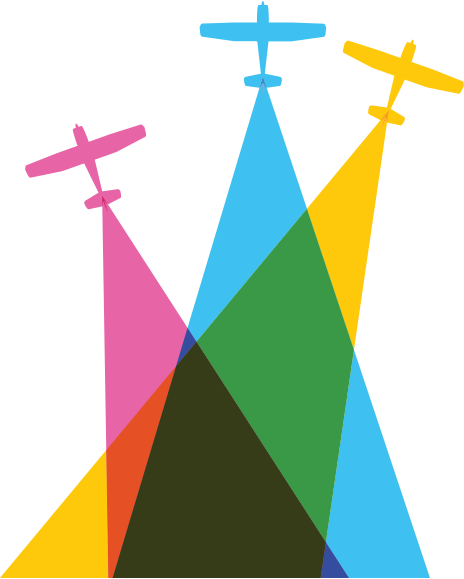
Oops!
We seem to have lost the page you were looking for...
We're sorry, but you encountered a 404 Error which means the page you are looking for doesn't appear to exist. Try returning to previous page and try again, or create a new search.
If this issue persists please contact our support staff at 1.800.USA.AOPA (1.800.872.2672) or 301.695.2000
Here are some helpful links instead: